What is Porosity in Welding: Vital Tips for Achieving Flawless Welds
What is Porosity in Welding: Vital Tips for Achieving Flawless Welds
Blog Article
Untangling the Mystery of Porosity in Welding: Tips for Lessening Issues and Taking Full Advantage Of Quality
In the intricate world of welding, porosity stays a relentless obstacle that can significantly impact the high quality and stability of bonded joints. Recognizing the factors that contribute to porosity formation is important in the pursuit of remarkable welds. By unraveling the mystery of porosity and executing efficient techniques for flaw reduction, welders can elevate the criteria of their job to attain superior top quality end results. As we explore the midsts of porosity in welding, revealing the keys to its avoidance and control will be critical for experts seeking to master the art of top quality weldments.
Recognizing Porosity in Welding
Porosity in welding, an usual issue experienced by welders, refers to the existence of gas pockets or voids in the bonded material, which can compromise the integrity and quality of the weld. These gas pockets are generally entraped during the welding process as a result of different factors such as incorrect shielding gas, infected base materials, or wrong welding specifications. The formation of porosity can deteriorate the weld, making it vulnerable to fracturing and rust, inevitably resulting in architectural failures.
Understanding the source of porosity is critical for welders to efficiently stop its occurrence. By identifying the significance of preserving correct gas protecting, making certain the tidiness of base products, and maximizing welding settings, welders can substantially reduce the probability of porosity development. Additionally, using methods like pre-heating the base product, employing appropriate welding strategies, and performing comprehensive assessments post-welding can better aid in reducing porosity flaws. On the whole, a comprehensive understanding of porosity in welding is vital for welders to create high-grade and durable welds.

Usual Reasons of Porosity
When evaluating welding processes for possible quality problems, understanding the typical reasons of porosity is vital for keeping weld integrity and protecting against structural failures. Porosity, identified by the existence of dental caries or voids in the weld steel, can dramatically compromise the mechanical buildings of a welded joint.
One more common reason for porosity is the presence of wetness and pollutants externally of the base steel or filler product. When welding products are not properly cleaned up or are subjected to high degrees of moisture, the evaporation of these contaminants throughout welding can develop gaps within the weld grain. In addition, welding at inappropriate parameters, such as excessively high travel speeds or currents, can generate extreme turbulence in the weld swimming pool, capturing gases and triggering porosity. By resolving these usual reasons via proper gas shielding, material prep work, and adherence to optimum welding criteria, welders can minimize porosity and enhance the quality of their welds.
Strategies for Porosity Avoidance
Carrying out effective safety nets is critical in decreasing the incident of porosity in welding processes. One strategy for porosity prevention is ensuring correct cleaning of the base metal before welding. Impurities such as oil, grease, corrosion, and paint can result in porosity, so thorough cleansing utilizing suitable solvents or mechanical approaches is necessary.

One more trick precautionary step is the option of the best welding consumables. Making use of top notch filler materials and protecting gases that are suitable for the base steel and welding process can substantially reduce the danger of porosity. Additionally, preserving correct welding specifications, such as voltage, existing, travel speed, and gas flow rate, is crucial for porosity avoidance. Departing from the advised settings can lead to inappropriate gas coverage and insufficient blend, leading to porosity.
Additionally, utilizing appropriate welding strategies, such as keeping a regular traveling rate, electrode angle, and arc size, can help prevent porosity (What is Porosity). Sufficient training of welders to ensure they comply with finest methods and quality assurance treatments is likewise necessary in decreasing porosity issues in welding
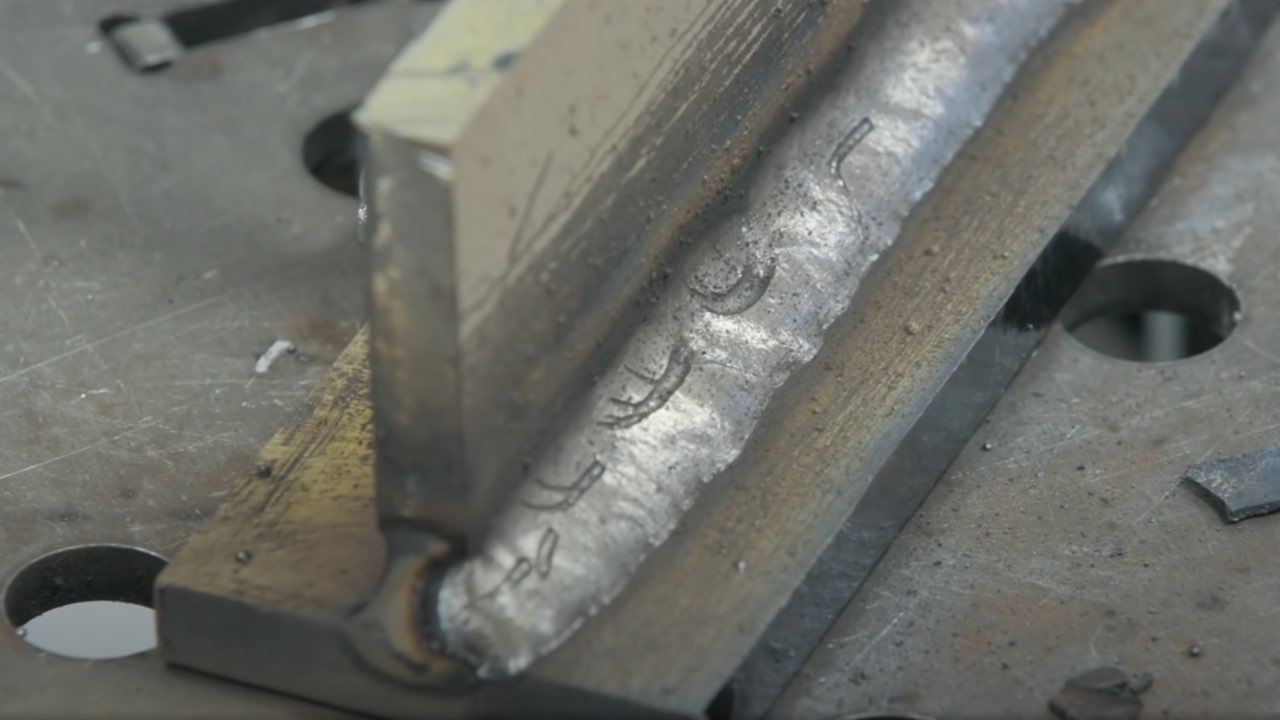
Best Practices for Top Quality Welds
Making certain adherence to sector criteria and appropriate weld joint preparation are fundamental aspects of attaining constantly top notch welds. Along have a peek at this site with these foundational actions, there are several best techniques that welders can carry out to even more enhance the top quality of their welds. One trick method is maintaining correct tidiness try here in the welding area. Impurities such as oil, grease, corrosion, and paint can negatively affect the top quality of the weld, causing defects. Extensively cleaning up the work surface and surrounding area prior to welding can help alleviate these issues.
An additional ideal technique is to meticulously pick the proper welding criteria for the certain products being joined. Proper parameter selection ensures optimum weld infiltration, combination, and general high quality. Using high-quality welding consumables, such as electrodes and filler steels, can dramatically influence the final weld quality.
Importance of Porosity Control
Porosity control plays a crucial duty in making sure the stability and quality of welding joints. Porosity, identified by the existence of tooth cavities or voids within the weld steel, can considerably compromise the mechanical properties and architectural stability of the weld. Too much porosity deteriorates the weld, making it much more susceptible to fracturing, rust, and total failure under functional tons.
Efficient porosity control is crucial for preserving the wanted mechanical residential or commercial properties, such as toughness, Get More Info ductility, and toughness, of the welded joint. What is Porosity. By lessening porosity, welders can boost the overall high quality and integrity of the weld, ensuring that it satisfies the efficiency needs of the desired application
Furthermore, porosity control is important for accomplishing the wanted visual look of the weld. Excessive porosity not only compromises the weld however likewise interferes with its aesthetic allure, which can be crucial in industries where aesthetics are essential. Appropriate porosity control methods, such as making use of the correct shielding gas, managing the welding criteria, and guaranteeing correct sanitation of the base products, are crucial for creating high-grade welds with minimal defects.
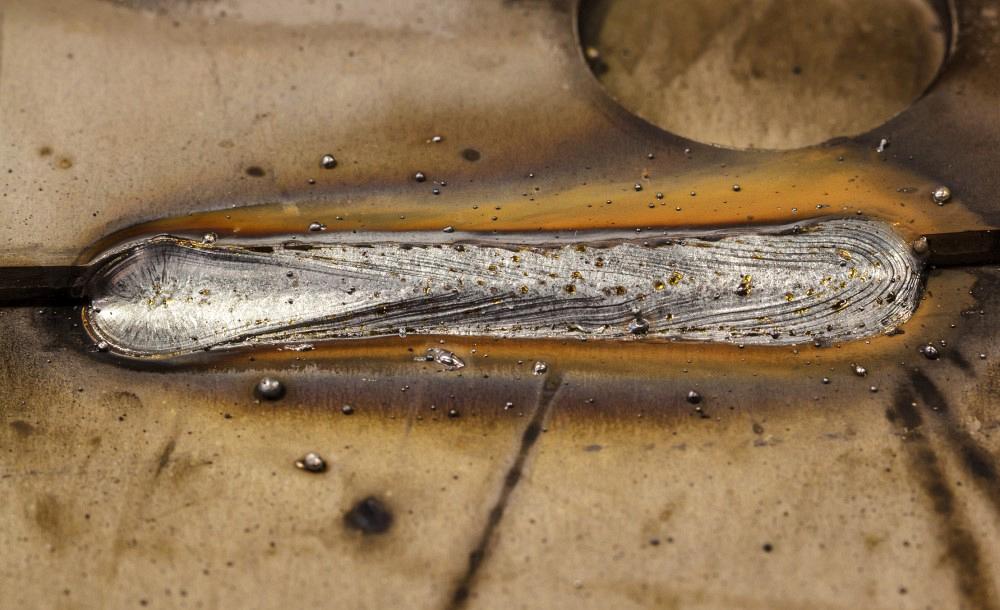
Conclusion
In conclusion, porosity in welding is an usual flaw that can compromise the high quality of the weld. It is vital to regulate porosity in welding to guarantee the honesty and stamina of the last product.
Report this page